Revolutionary designs and low-profile stacking make for more efficient satellites and add new opportunities in space. Evolving from the simple cubesat and the Mars Curiosity era, we are seeing revolutionary methods in satellite construction. New component devices are offering improved solutions to our space industry from communication and location management to surveillance, research and deeper space travel.
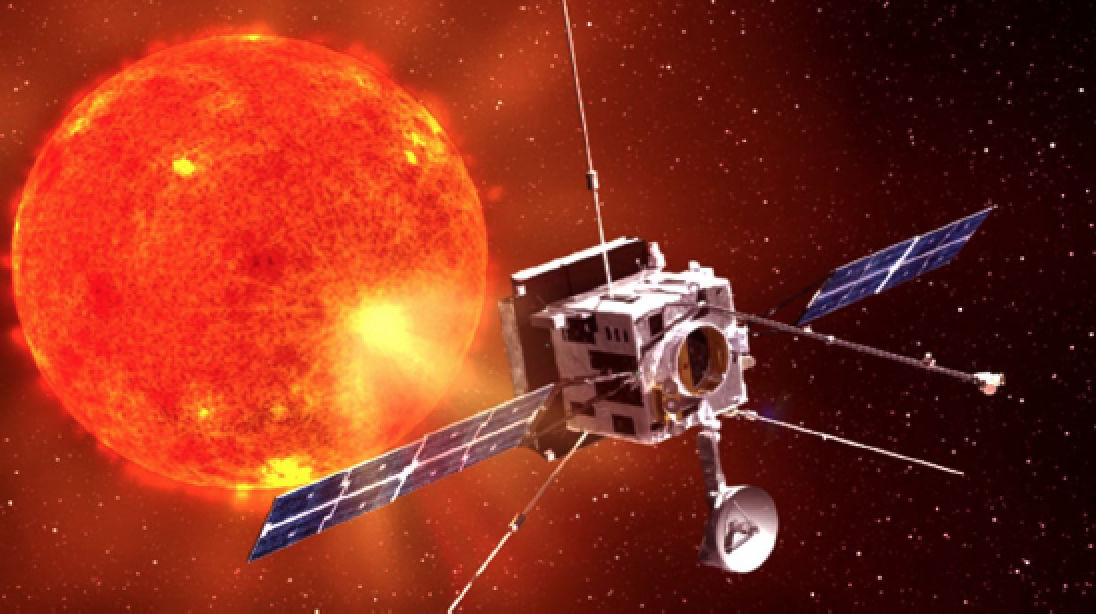
The new Solar Orbiter is a collection of work from countries around the world and is collecting data images from its STIX (Spectrometer/Telescope for Imaging X-Rays) and its EUI (Extreme Ultraviolet Imager). The goal is to understand more about solar flares, hot spots, gamma radiation bursts and how that affects us on Earth.
The electronic components, connectors and cable used within the Solar Orbiter were selected to support a variety of new scientific analysis systems from RF to X-radiation, while operating under extreme thermal challenges. A number of the interconnections required had to be quite small and rugged.
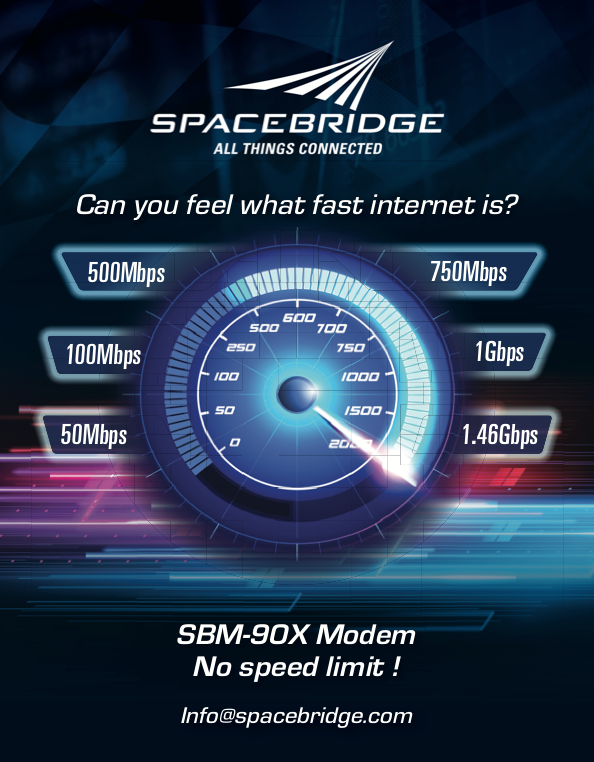
Space qualified Nano-D connectors meet the specifications needed to survive operation within the system and be mounted on the probe of the STIX telescope. PZN connectors were selected for board-to-wire interconnections and are being used to match size and weight reductions of high-density performance.
The PZNs also provided a low-profile interconnection system that improved dense packing of the electronics. The PZNs beryllium copper spring pins, at .025” pitch, are plated with nickel and gold, offering continuous signal integrity through extreme shock and vibration. Reaching from process boards to sensors, detectors and actuators can carry up to 1 ampere of current in the Teflon® insulated wiring.
Larger satellites are also embracing newer, high density electronics: modules are being powered by advanced CMOS silicon, Gallium Arsenide, Gallium Nitride and even MEM, electro-mechanical chip technologies.
Satellite weight and size are dramatically reduced simultaneously as functional capability increases.The newer chip technologies can also provide the satellite with more data collection, faster signal processing and low energy satellite position and control systems at significantly reduced voltage and current levels. This extends the power supply life and reduces the level of power collection required and stored on the satellite itself.
Space system designers can launch more satellites for significantly lower costs and even put extra or back-up satellites in space for later use. Individual satellite repair may evolve to enable the process of in-space replacement of components and remote programming while destroying those satellites that are unable to function.
As cubesat signals now operate at lower voltage and lower current levels, heat is reduced.This allows squeezing in additional circuitry.The standard 10cm cube with defined mass of 1.33 kilograms per unit can also be stacked into multiple 2U and 3U cubes to fit within a taller frame.
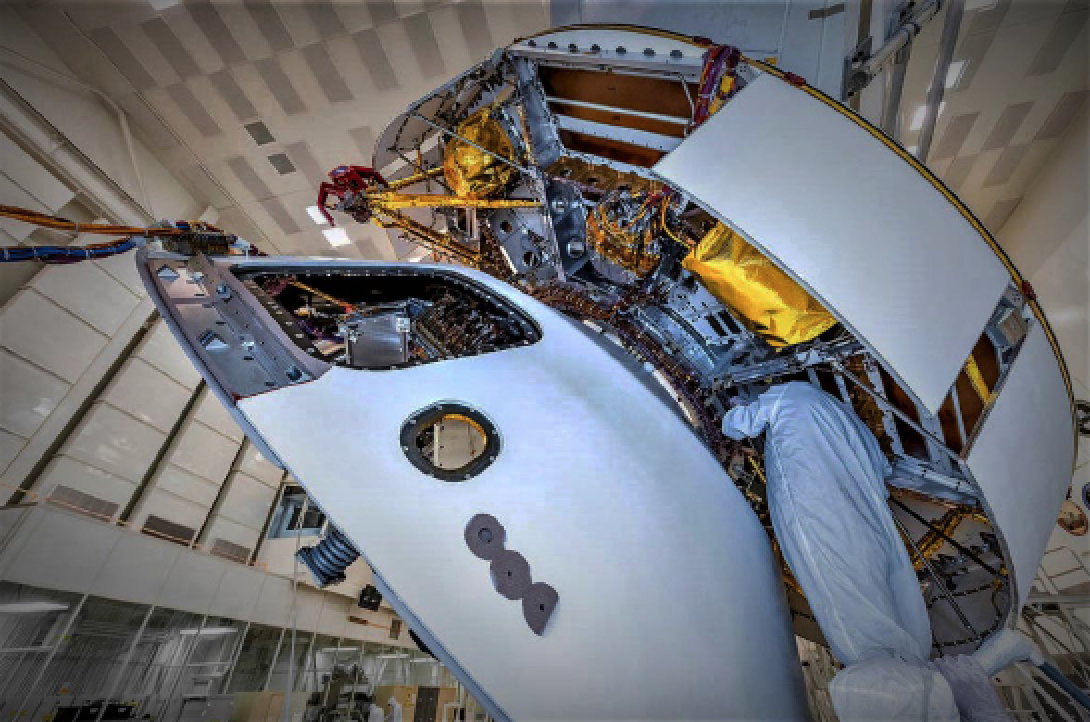
These modular stacked sets of cubesat units are assembled and then loaded, transferred into space and released using launch tools such as the NASA Launch device, or the “ISIPOD CubeSat Deployer” that is used by the European Space Agency. As cubesat increases circuit density, multiple new functions, wiring and connectors become a critical, neural network within each cube as well as from cube to cube. An electrical network of interconnections from circuit to circuit, from power source to circuit and from sensors to detectors, must fit into the platform.
Wiring and signal protection technology in all satellite sizes have become a serious part of the process of doing more in less space... while in space. For example, surveillance data collected on the satellite is transferred using high-speed, differential, digital signaling at rather low voltage levels.
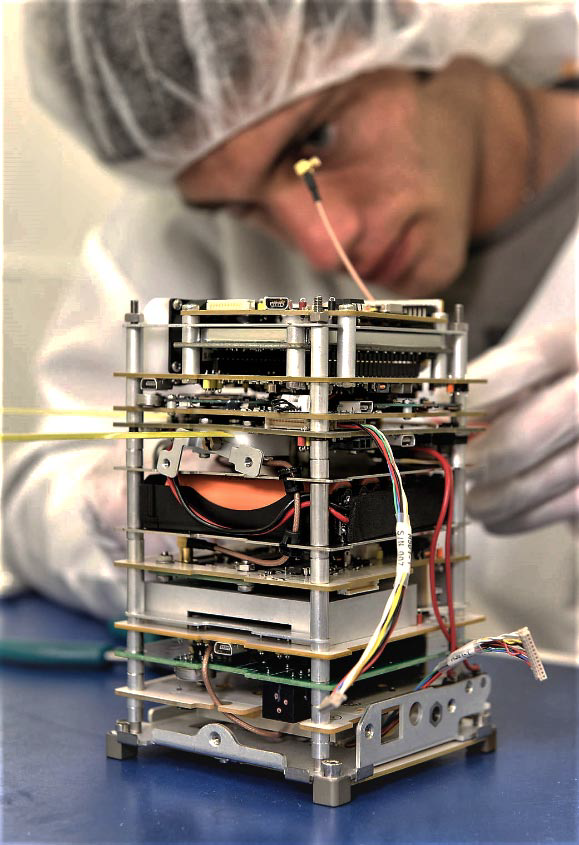
System EMI (electromagnetic interference) can penetrate cable shielding, adding noise that compromises the data. Lower voltage signal-swing can be compromised by physical changes that affect the cable impedance due to tight routing inside the cube stack.
RF data must be run on high quality, micro-sized, coaxial connectors and cable must be made and qualified to NASA specification 8736.4. Space grade connectors must offer an exact fit within the miniature, physical design and offer sustained physical reliability from lift-off to long term flight.
Low, outgassing materials are required to prevent circuit degradation and must survive extreme temperature variations. In cubesats, PZN connectors for board to wire lines are being used to match size and weight reduction with NASA expectations for high density performance. The low weight and rugged performance of “Space Grade” Nano-D connectors are often selected for increased density and reliability.
These MIL-DTL-32139 nano-miniature connectors are approved for space programs and inspected per EEE-INST-002. All materials exceed the NASA outgassing specifications and perform well during deep space travel that endures significant thermal cycles.
Nano-D connectors, at .025" pitch, have reduced size and weight by as much as four times that of standard micro-D connector and eight times that of previous D-sub footprints.Nano-Ds are polarized and shrouded by liquid crystal polymer insulators. The pin-to-socket strength and “lobed” housing alignment system makes these connectors capable of more than 2,000 mating cycles.
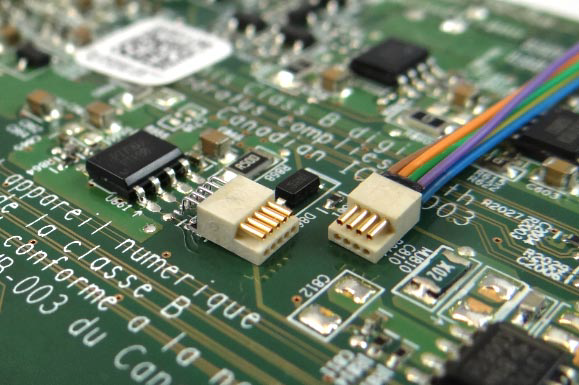
Multiple pin counts and mixed signals can be built-into one connector to reduce the number of cables running from one module to another. Board-mount options include both surface-mount and through-hole variations.
Wire and cable are designed to exactly meet the design needs of the system. Space connector shell finishes include nickel-plated aluminum, stainless steel, and titanium depending on the system designer.
Connector selection design and testing is a critical item for engineers in the correct selection for space products. They should depend on specifications such as the NASA specification EEE-INST-002. This instrument provides instruction on selecting, screening and qualifying parts for use on NASA GSFC space projects.
Most space-certified connector companies offer NASA screening per EEE-INST-002. Table 2J in the NASA spec contains specific inspection instructions for Nano-Sized connectors. These additional screening requirements exceed some earlier points within the MIL-DTL-32139.
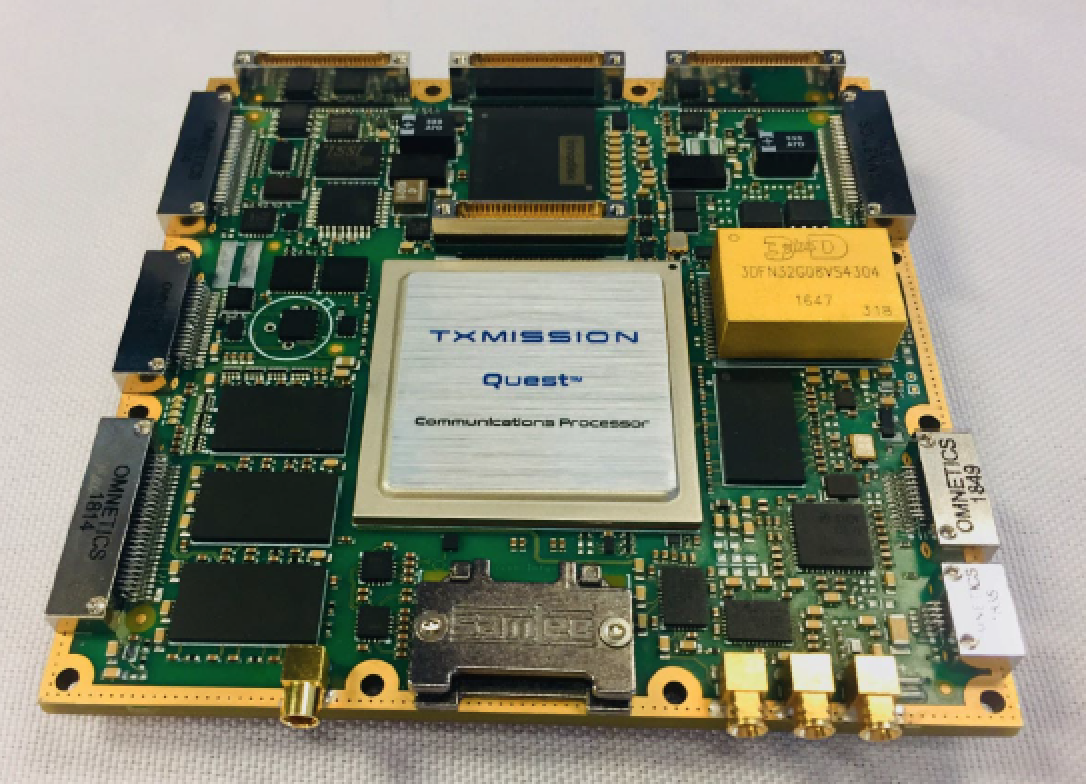
NASA defines three levels of screening:
• Level 1 for the highest level of reliability or for applications deemed mission-critical
• Level 2 for high reliability
• Level 3 for standard reliability.
Designers are wise to work with connector manufacturers that adhere to these screening levels.
The Curiosity Rover is operating on Mars today and is now awaiting arrival of the Perseverance. Significant additions for control, data transmission and especially soil and environmental analysis are expected from the Perseverance program. Advanced electronics for data gathering, analysis and data storage offer an exciting opportunity.
Omnetics and other Space Qualified Connector suppliers are poised to offer unique connector and cable systems designed to an application’s specific needs. Today’s solid modelling systems offer nearly immediate imagery that exhibits how the interconnects can fit within new structures.
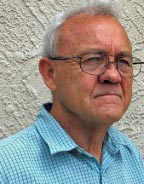
New 3-D material models are built within a couple of days for trial pieces to fit neatly into cramped size and shapes. Satellite system designers are encouraged to call connector developers and look into the standard connectors available that can be used or quickly modified to enhance their system layout.
www.omnetics.com
Author Bob Stanton is the Director of Technology for Ommetics Connector Corporation.